Zine Printing Tips From a Solopreneur
Zines (self-produced, small-circulation publications) are extremely DIY, and therefore punk- and hacker-adjacent by nature. While they can be made with nothing more than a home printer or photocopier, some might benefit from professional production while losing none of their core appeal. However, the professional print world has a few gotchas, and in true hacker spirit [Mabel Wynne] shares things she learned the hard way when printing her solo art zine.
As with assembling hardware kits, assembling a zine can take up a lot of physical table space.
[Mabel] says the most useful detail to nail down before even speaking to printers is the zine’s binding, because binding type can impact layout and design of an entire document. Her advice? Nail it down early, whether it’s a simple saddlestitch (staples through a v-shaped fold of sheets), spiral binding (which allows a document to lay flat), or something else.
Aside from paper and print method (which may be more or less important depending on the zine’s content) the other thing that’s important to consider is the finishing. Finishing consists of things like cutting, folding, and binding of the raw printed sheets. A printer will help arrange these, but it’s possible to do some or even all of these steps for oneself, which is not only more hands-on but reduces costs.
Do test runs, and prototype the end result in order to force unknown problems to the surface before they become design issues. Really, the fundamentals have a lot in common with designing and building kits or hardware. Check out [Mabel]’s article for the full details; she even talks a little about managing money and getting a zine onto shelves.
Zine making is the DIYer’s way to give ideas physical form and put them into peoples’ hands more or less directly, and there’s something wonderfully and inherently subversive about that concept. 2600 has its roots in print, but oddball disk magazines prove one doesn’t need paper to make a zine.
hackaday.com/2025/07/25/zine-p…
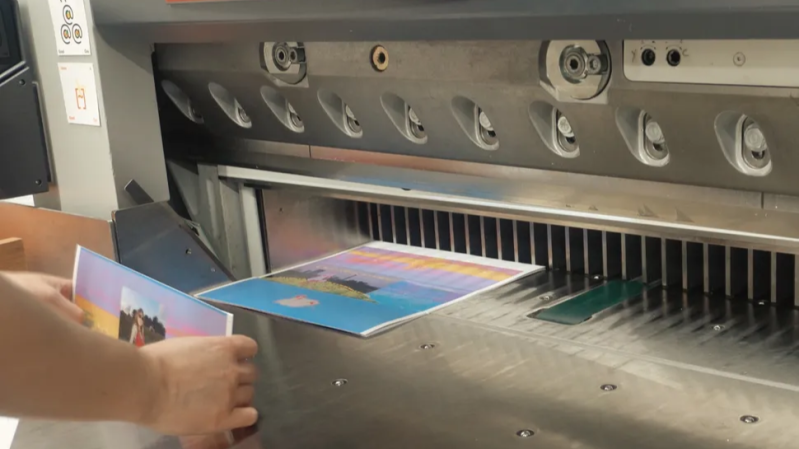
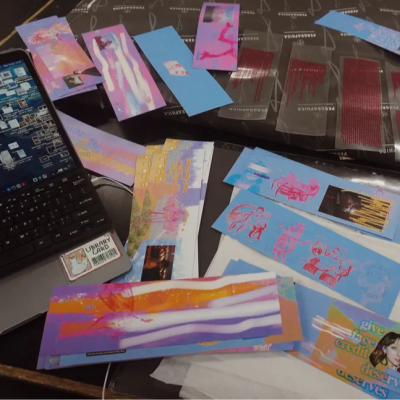
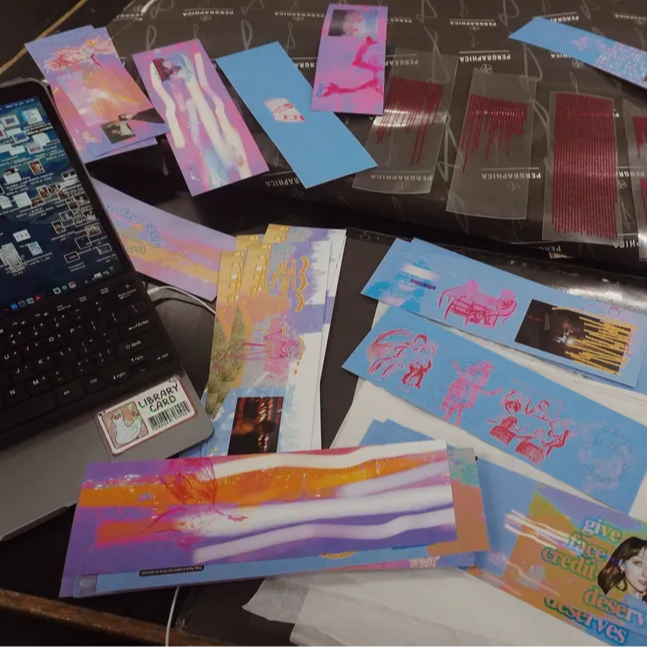